HVAC Costs Could Cool Commercial Real Estate Deals
In an era of global uncertainty, few systems feel the heat of economic volatility like Heating, Ventilation, and Air Conditioning (HVAC). These systems are essential for every type of building, especially in the world of industrial space, office space, and retail development. Yet their behind-the-scenes role makes it easy to overlook their significance until costs spike, installations stall, or maintenance becomes prohibitively expensive. As global supply chains continue to adjust to post-pandemic shifts and trade tariffs reemerge, the cost and availability of HVAC components are under pressure. This has created unexpected challenges in the process of securing and completing commercial real estate deals.
Whether you’re a commercial real estate agent navigating tenant expectations, an investor underwriting development costs, or a professional involved in commercial property management and building operations, HVAC-related price surges are not just a facilities issue. They have become a critical factor influencing deal timelines, buildout budgets, and even lease negotiations.
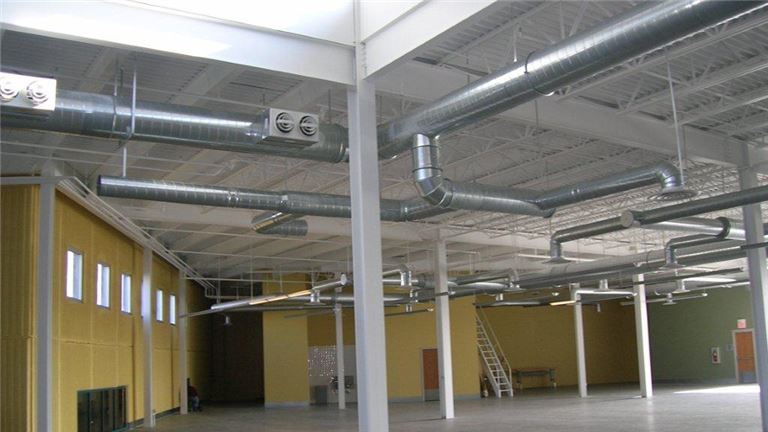
HVAC Systems Depend on a Complex Global Supply Chain
Modern HVAC systems rely on components sourced from all over the world. Compressors might be manufactured in China, copper coils sourced from Mexico, fans assembled in Germany, and control systems developed in the United States. The HVAC supply chain is a tightly choreographed global operation that depends on reliable trade routes, efficient manufacturing timelines, and predictable tariff policies.
COVID-19 highlighted how vulnerable this ecosystem truly is. Factory shutdowns in Asia, port backlogs in North America, and container shortages across the globe disrupted manufacturing and slowed the delivery of vital HVAC parts. Even as the world reopened, the residual impact lingers in the form of longer lead times and rising prices.
Layer on top of this the evolving tariff landscape. The reimposition of tariffs on Chinese imports, potential new tariffs under Section 301 investigations, and renewed emphasis on domestic reshoring all affect the cost structures for imported HVAC components. These changes can significantly inflate the cost of building improvements, tenant buildouts, and system replacements, especially in older industrial and office space stock that may already require infrastructure upgrades.
Rising HVAC Costs Complicate Real Estate Development and Leasing
The real estate sector is particularly sensitive to fluctuations in HVAC costs because HVAC is one of the most capital-intensive components of tenant improvements and building operations. Whether it’s a logistics center leasing industrial space or a corporate tenant moving into a new office suite, HVAC installation and efficiency are core to occupancy readiness and operating cost projections.
When costs spike or equipment delivery is delayed, deals can stall. Construction timelines are extended. Tenant improvement allowances are exceeded. And negotiations over who bears the additional cost—landlord or tenant—become more contentious.
For commercial real estate agents, these uncertainties can introduce friction into what were once straightforward leasing discussions. A tenant expecting a five-month delivery timeline might be looking at eight months or longer due to a backordered rooftop unit. Suddenly, “move-in ready” doesn’t mean what it used to.
For developers, the numbers can get even tighter. Speculative industrial developments that pencil out at one HVAC unit cost may suddenly find their pro formas off-balance when that same system costs 20 percent more and takes twice as long to arrive. That hits the bottom line and introduces risk to sale or lease assumptions.
Energy Efficiency Mandates Add Pressure
New energy efficiency regulations are also shaping the HVAC market. The U.S. Department of Energy recently updated minimum efficiency standards for commercial HVAC equipment. While these changes aim to improve long-term sustainability and reduce energy usage, they also make systems more complex and expensive in the short term.
More advanced systems require more sophisticated components, often from specific global suppliers. If one piece of that supply chain is disrupted by tariffs or logistical challenges, it can derail the entire project timeline. And because these newer systems must be installed to meet code, there is no option to downgrade to a simpler, cheaper solution.
For commercial property management professionals, this presents a difficult challenge. They must maintain comfort and compliance while managing increasing repair costs and capital expenditure expectations. Budgeting for HVAC system replacement now requires not just understanding system age, but anticipating trade policy and supply chain dynamics as well.
Industrial Space is Particularly Vulnerable
Industrial real estate, especially in warehousing, cold storage, and light manufacturing, depends heavily on HVAC systems. From temperature-controlled logistics to climate-sensitive assembly processes, air handling and conditioning are not luxuries—they’re core infrastructure.
As e-commerce continues to grow and reshoring of manufacturing accelerates, demand for well-ventilated, temperature-stable industrial space is on the rise. But if HVAC systems become cost-prohibitive or difficult to install, landlords may face difficulty upgrading older inventory to meet the needs of modern tenants. This could reduce competitiveness, increase vacancy durations, or push deals toward newer, more expensive developments.
This pressure is particularly acute in tight industrial markets with limited new supply. In those areas, the availability and cost of HVAC components may be the difference between signing a lease or losing a tenant to a competing property.
What Commercial Real Estate Agents and Owners Can Do
Navigating this environment requires both foresight and agility. Commercial real estate agents should begin conversations with HVAC timelines and costs in mind, setting expectations with both landlords and tenants. Discussing buildout constraints early can help avoid surprises later in the process.
Landlords and developers should work closely with mechanical contractors to pre-order long-lead HVAC systems when possible, or explore temporary solutions to bridge installation delays. Exploring domestic or alternative suppliers may provide some insulation against geopolitical disruptions and tariffs.
Commercial property management teams should be actively auditing HVAC systems across their portfolios to identify units near end-of-life and plan replacements accordingly. Proactive upgrades may help avoid last-minute emergency repairs that are now more expensive and harder to schedule.
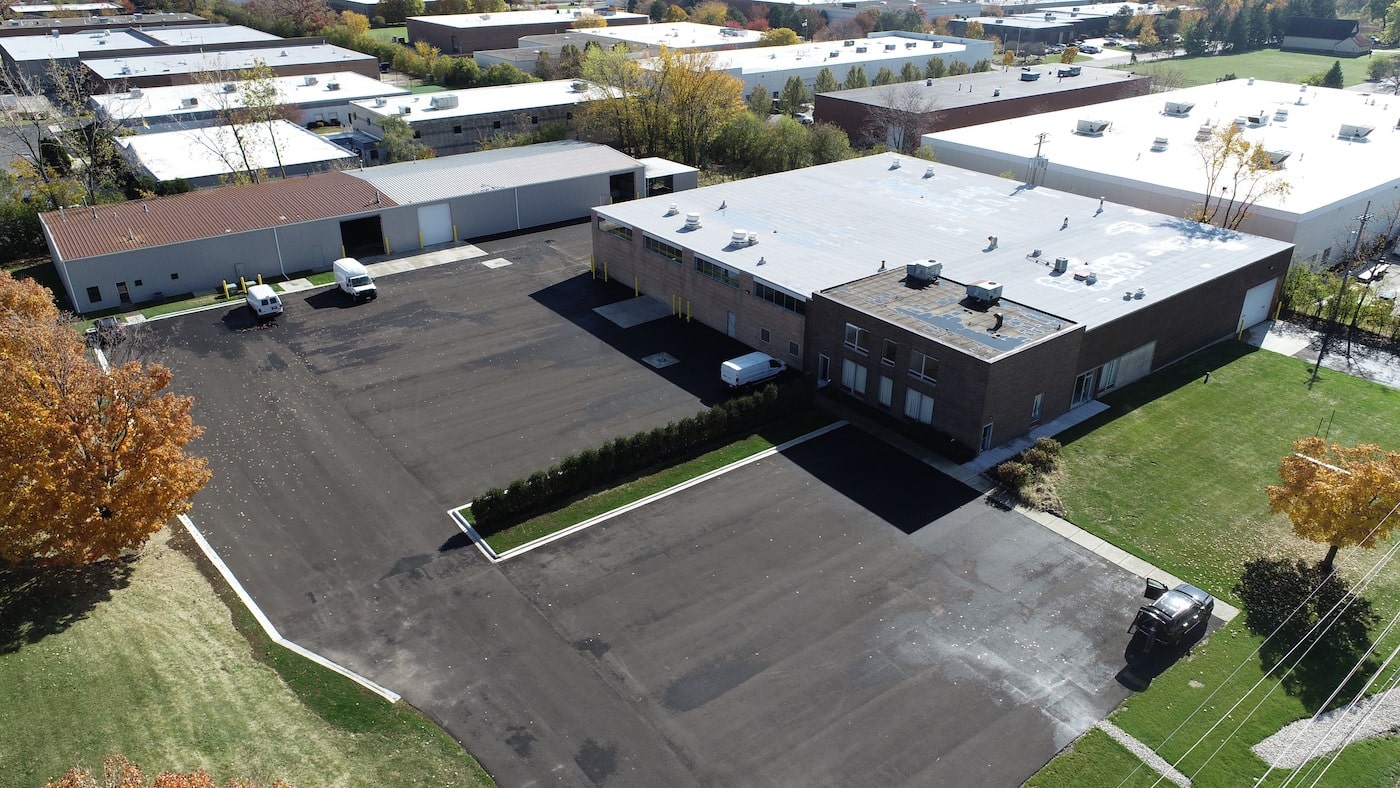
Conclusion: HVAC is No Longer a Background Issue
What was once considered a background utility is now a front-and-center risk factor in commercial real estate deals. The combination of a strained global supply chain and shifting trade policies means HVAC costs are rising, and timelines are increasingly unpredictable. These pressures touch every part of the industry, from commercial property management to industrial development and office space leasing.
In this climate, having a knowledgeable commercial real estate agent who understands these dynamics isn’t optional—it’s essential. Getting deals done today means understanding not just the rent roll or location but the real-world constraints that affect tenant improvements, operating budgets, and building performance.
For landlords, investors, and users alike, the new HVAC equation is about more than air. It’s about timing, cost, compliance, and ultimately, deal execution.